June quarterly 2011 activities report highlight
Closed-loop salt slag recycling operations have commenced. This is a significant milestone for the company,
paving the way for the global expansion of the technology
paving the way for the global expansion of the technology
first shipment of AL80, an aluminium oxide product, has been prepared and is awaiting departure. The
first shipment is 800 tonnes and will be followed by monthly shipments of a minimum of 1,500 tonnes.
first shipment is 800 tonnes and will be followed by monthly shipments of a minimum of 1,500 tonnes.
During the quarter, Alreco also received additional enquiries for offtake of a substantial monthly tonnage of
AL80 from another party.
AL80 from another party.
crystalliser technology provider has indicated that the system will be operational by the end of December 2011.
It is expected that this first plant will
have a throughput of 200,000 to 250,000 tonnes per annum, representing an estimated 20-25% of the salt slag
produced by the entire US aluminium industry. It is understood that an additional two to four salt slag recycling
plants could be justified in the United States.
have a throughput of 200,000 to 250,000 tonnes per annum, representing an estimated 20-25% of the salt slag
produced by the entire US aluminium industry. It is understood that an additional two to four salt slag recycling
plants could be justified in the United States.
MHM has also recently engaged with aluminium companies that are showing keen interest to supply salt cake to a second salt slag recycling facility in a region to service the north-eastern United States and parts of Canada.
the first of the contracts may be signed by the end of August 2011, and has recently hosted
a number of potential US salt slag suppliers for site visits in Geelong.
a number of potential US salt slag suppliers for site visits in Geelong.
Site acquisition has taken a little longer than initially anticipated. In May and June, MHM conducted extensive
due diligence, agreed a purchase price and finalized terms for a property purchase contract for an 80-acre site in
Tennessee that showed great potential. However, sub-surface environmental assessment by MHM indicated
that the site contained some geotechnical issues and consequently it was decided to seek alternatives.
due diligence, agreed a purchase price and finalized terms for a property purchase contract for an 80-acre site in
Tennessee that showed great potential. However, sub-surface environmental assessment by MHM indicated
that the site contained some geotechnical issues and consequently it was decided to seek alternatives.
MHM has general terms of a financial support package, however the final
details will depend on site selection.
details will depend on site selection.
A number of meetings and presentations with US investors were held during the quarter, which were well
received. Additional presentations are planned in due course, particularly following execution of US salt slag
supply contracts and Tennessee land acquisition.
received. Additional presentations are planned in due course, particularly following execution of US salt slag
supply contracts and Tennessee land acquisition.
MHM continues to work with a number of parties concerning offtake of lump silica and silica flour, both for
export and for utilisation in a proposed Tasmanian silicon smelter.
export and for utilisation in a proposed Tasmanian silicon smelter.
June quarterly 2011 cash flow report
Gross cash receipts $1,133,000
Gross Operating cash surplus $46,851
Trade receivable $1,200,000
cash at end of June $9.021m
Below are my opinions and views
Financial
March quarterAs shown on cashflow report
Revenue $886,000
alu. processing exp. -$756,000
gross operating cashflow -$756,000
June quarter
As shown on cashflow report
Revenue $1,133,000
alu. processing exp. -$936,000
gross operating cashflow -$531,000
============================================
June operating cash flow is +$46,851
that means trade receivable from March quarter is $46,851 + $531,000 = $577,851
trade receivable in June is $1.2m
actual revenue in June should be $2,333,000
alu. processing exp. -$936,000
so that's $2.49 rev./$1 cost in June quarter
and $1.94 rev./$1 cost in March quarter
Estimation for Sep. Quarter
Based on the estimated production cost -$895,000
use the $2.49 rev./$1 cost in June and assume 48.56% of the revenue will be received in current quarer
estimated revenue in current quarter $2,228,550
48.56% of it is $1,082,275
plus
trade receivable in June $1,200,000
plus
revenue from 3,800 tonnes of AL80
AU$330 x 3,800 = $1,254,000
Then at end of current quarter, MHM should have revenue of
$3,536,275
Profitability
For aluminium processing activities only
March quarter: profit $707,851
June quarter: profit $1,397,000
Sep. quarter: profit $2,587,550 (est.)
Fundamental
Australia operation
1. AL80 revenues in September quarter
2. Possible new AL80 off-take contract to be signed
3. crystallization begin in end of 2011
4. Potential carbon tax benefit
5. Revenue and profit should increase significantly once the AL80 sales begin.
US operation
1. US supply contracts should be signed by end of August
2. Government support should be granted once the site selection been finalized
3. Discussion with other aluminium companies for potential 2nd salt slag recycling plant in the state
4. Contamination fund in the SSC mono landfill, this shouldn't affect the supply as the total aluminium salt slag produced in US is around 1,000,000 tonnes
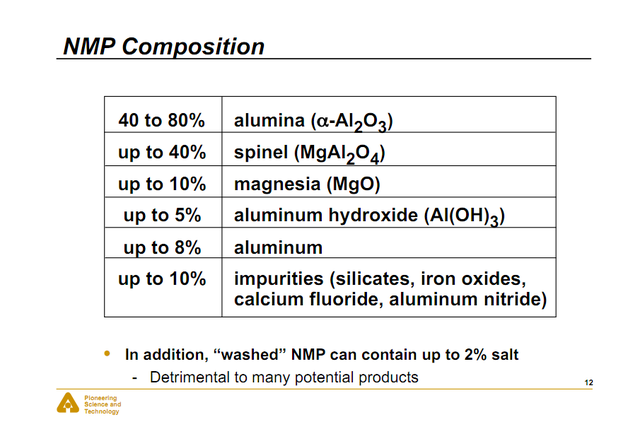
Phases of Alumina
Aluminium oxide exists in many forms,

Commercial Grades of Alumina
Smelter Grade Alumina
Smelter or metallurgical grade alumina is the name given to alumina utilised in the manufacture of aluminium metal. Historically it was manufactured from aluminium hydroxide using rotary kilns but is now generally produced in fluid bed or fluid flash calciners. In the fluid flash processes the aluminium hydroxide is fed into a counter-current stream of hot air obtained by burning fuel oil or gas. The first effect is that of removing the free water and this is followed by removal of the chemically combined water; this occurs over a range of temperatures between 180-600oC. The dehydrated alumina is principally in the form of activated alumina and the surface area gradually decreases as the temperature rises towards 1000oC. Further calcination at temperatures > 1000oC converts this to the more stable a-form. The conversion to the a-form is typically of the order of 25% and the specific surface area is relatively high at >50m2/g due to the presence of transition aluminas.
Calcined Alumina
If aluminium hydroxide is heated to a temperature in excess of 1100oC, then it passes through the transition phases of alumina referred to above.
The final product, if a high enough temperature is used, is a-alumina. The manufacturing process is commercially undertaken in long rotary kilns. Mineralisers are frequently added to catalyse the reaction and bring down the temperature at which the a-alumina phase forms; fluoride salts are the most commonly used mineralisers.
These calcined alumina products are used in a wide range of ceramic and refractory applications. The main impurity present is sodium oxide. Various grades are produced which differ in crystallite size, morphology and chemical impurities.
The calcined grades are often sub-divided into ordinary soda, medium soda (soda level 0.15-0.25% wt%) and low soda alumina.
Low Soda Alumina
Many applications, particularly in the electrical/electronic areas, require a low level of soda to be present in the alumina. A low soda alumina is generally defined as an alumina with soda content of <0.1% by weight. This can be manufactured by many different routes including acid washing, chlorine addition, boron addition, and utilisation of soda adsorbing compounds.
Reactive Alumina
Reactive alumina is the terms normally given to a relatively high purity and small crystal size (<1 mm) alumina which sinters to a fully dense body at lower temperatures than low soda, medium-soda or ordinary-soda aluminas. These powders are normally supplied after intensive ball-milling which breaks up the agglomerates produced after calcination. They are utilised where exceptional strength, wear resistance, temperature resistance, surface finish or chemical inertness are required.
Tabular Alumina
Tabular alumina is recrystallised or sintered a-alumina, so called because its morphology consists of large, 50-500 mm, flat tablet-shaped crystals of corundum. It is produced by pelletising, extruding, or pressing calcined alumina into shapes and then heating these shapes to a temperature just under their fusion point, 1700-1850oC in shaft kilns.
After calcination, the spheres of shapes of sintered alumina can be used as they are for some applications, e.g. catalyst beds, or they can be crushed, screened and ground to produce a wide range of sizes. As the material has been sintered it has an especially low porosity, high density, low permeability, good chemical inertness, high refractoriness and is especially suitable for refractory applications.
Fused Alumina
Fused alumina is made in electric arc furnaces by passing a current between vertical carbon electrodes. The heat generated melts the alumina. The furnace consists of a water cooled steel shell and 3-20 tonne batches of material are fused at any one time. The fused alumina has a high density, low porosity, low permeability and high refractoriness. As a result these characteristics, it is used in the manufacture of abrasives and refractories.
High Purity Aluminas
High purity aluminas are normally classified as those with a purity of 99.99% and can be manufactured by routes starting from Bayer hydrate using successive activations and washings, or via a chloride to achieve the necessary degree of purity. Even higher purities are manufactured by calcining ammonium aluminium sulfate or from aluminium metal. In the case of the route via ammonium aluminium sulfate, the necessary degree of purity is obtained by successive recrystallisations. Especially high purities can be made from aluminium by reacting the metal with an alcohol, purifying the aluminium alkoxide by distillation, hydrolysing and the calcination. A minor route involves subjecting super purity aluminium metal pellets under distilled water to a spark discharge.
Applications include the manufacture of synthetic gem stones such as rubies and yttrium aluminium garnets for lasers, and sapphires for instrument windows and lasers.
Alumina (Aluminium Oxide) - The Different Types of Commercially Available Grades
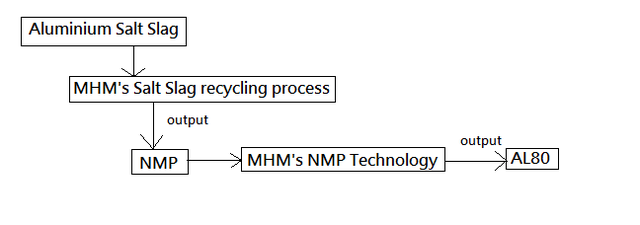
No comments:
Post a Comment